Business in 2018
Stability, profitability, growth
Sandvik Machining Solutions has been stable and profitable for many years and in 2018 we intensified our focus on profitable growth. Apart from the Metrologic acquisition, we also made a number of strategic acquisitions, such as privately-owned US-based company Dura-Mill, a manufacturer of precision solid carbide end mills and Chinese company Kunshan Ousike Precision Tools, a leading supplier of solid carbide round tools.
Efficiency and continuous improvements
Even in times of profitability and growth, we continue to work with efficiency and cost measures such as operational excellence and lean to alleviate bottlenecks or areas where we have unnecessary costs. This ensures we have a good base in the event of an economic downturn and it also frees up resources to invest in growth areas.
As a part of our ongoing work with operational excellence, we monitor our production footprint and capacity worldwide in order to adapt to global and local market conditions. In line with this we announced that the supply of ready to press (RTP) powder from the Coventry UK production unit will be phased out over the next three years. In 2018 we also announced the intention to close our insert production in Fondettes, France.
2018 in figures
Revenues: 40,343 million SEK ( 35,777) with 7.7% organic growth
Operating profit: 9,872 million SEK (8,413)
Operating margin: 24.5% (23.5)
Return on capital employed: 36.9% (35.0)
Employees: 19,284 (18,7451))
Gender balance: Men 79%, Women 21%
President: Klas Forsström
Lost time injury frequency rate (LTIFR): 1.7 (1.8)
Total recordable injury frequency rate (TRIFR): 3.0 (4.2)
Estimated market size: 200 billion SEK
1) Number of employees adjusted for items affecting comparability, due to internal reallocation.
Revenues by customer segment
Revenues by market area
Sustainable business
Sandvik Machining Solutions is focused on lowering its environmental impact by reducing waste and carbon dioxide emissions through better energy efficiency. Our efforts include using more LED technology, solar panels and district heating solutions. We are also optimizing our manufacturing processes for better efficiency and less waste. Our production plant in Gimo, Sweden converted from heating oil to district heat produced from biofuel. The new district heating solution is expected to reduce the plant’s greenhouse gas emissions by 1,850 tons, which is equivalent to the amount of heat required to heat 230 average single-family homes on a yearly basis.
We are also developing products that help our customers increase their productivity. For example, PrimeTurning™, a method that enables turning in all directions, results in a more than 50 percent increase in productivity compared to conventional turning. In addition to increasing production efficiency, our digital tools address waste across the machining value chain, simplifying Computer Numerical Control (CNC) programming and helping to reduce tool inventory and transport. Our in-machining metrology and adaptive process control efforts also lead to a reduction of scrap material.
In our production chain we can both regrind and recycle cemented carbide tools. We have local buy-back programs for used tools, such as inserts and solid carbide tools, and our Wolfram Bergbau und Hütten site in Austria recycles cemented carbide that goes back into the production of new tools.
The journey ahead
Sandvik Machining Solutions is transitioning from being a world-leading player in the industry of metal cutting, to becoming a leading solutions provider for the wider component manufacturing industry. With our technology and innovation capabilities, we see many opportunities for growth, both within our core metal cutting business as well as into areas such as digital manufacturing and additive manufacturing.
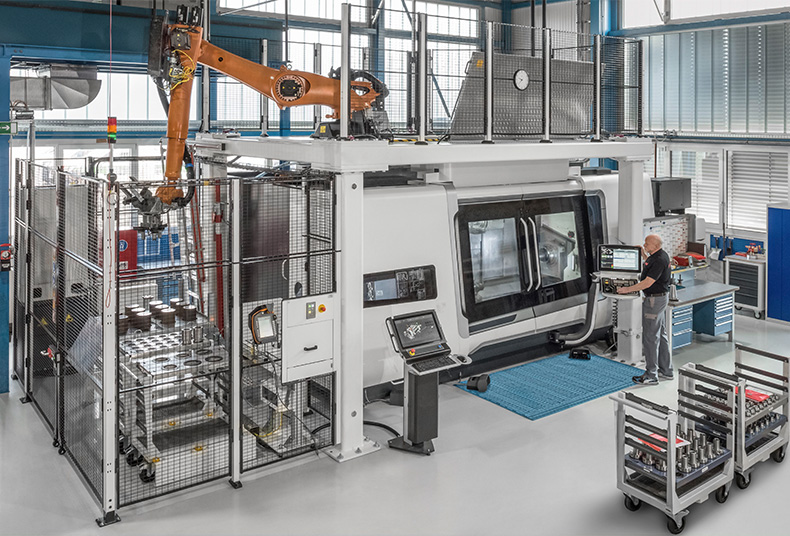
Sandvik’s highly automated production site in Renningen, Germany.