Innovations creating customer value
We increase customer productivity and make customers’ operations more efficient and sustainable with our technologically advanced products and solutions. These include innovations to automate and optimize manufacturing processes across the value chain.
In 2022 Sandvik launched the high-feed milling solution CoroMill® MH20, which delivers best-in-class edge security for a variety of industries. Particularly suited for machining aerospace components, it assures a longer tool life and a quicker machining process with less scrap, downtime and inventory.
CoroMill Dura (based on technology from previously acquired DuraMill) from Sandvik Coromant is a complete range of solid carbide end mills which significantly breaks up harmonics and reduces chatter and vibration. The end mills work in a wide range of applications and materials and provide greater machine flexibility, leading to reduced set-up time and reduced stock holding.
The next-generation Helical Turbo 16™ milling cutters from Seco combine top performance with ease of use. The larger cuts and higher feeds reduce cycle times, speed up production resulting in fewer inserts being needed. The replacement of nickel cutter coatings with a thin-film coating, also known as physical vapor deposition (PVD), a process in which a solid material is vaporized in a vacuum and deposited onto the surface of a part, increases sustainability.
A new metal powder from Wolfram, Bergla®, is produced from 100 percent recycled tungsten raw materials, which results in 90 percent less CO2 emissions compared to the use of primary sources. The powder composition, consisting of more than 95 percent tungsten carbide, can be customized to advance specific end-product attributes.
Sandvik launched 3D-printed cemented carbide, which provides superior wear resistant properties. Due to its extreme hardness, cemented carbide has been very challenging to machine, not least in complex geometries. 3D printing offers design freedom, decreased material waste, reduced lead times, optimized performance – and components lasting up to 20 times longer.
In 2022 we developed a new solution combining the ZeroTouch® Flexible Metrology Platform from DWFritz with Metrologic Group’s software Metrolog® X4. Non-contact, 3D measurement of parts is integrated near or in-line, resulting in inspection times one tenth of the time it takes with traditional methods. The solution measures complex features, creates a digital twin of a part and uses a 3D point cloud solution to ensure quality during the manufacturing process. Multiple machine orders have been received from key customers.
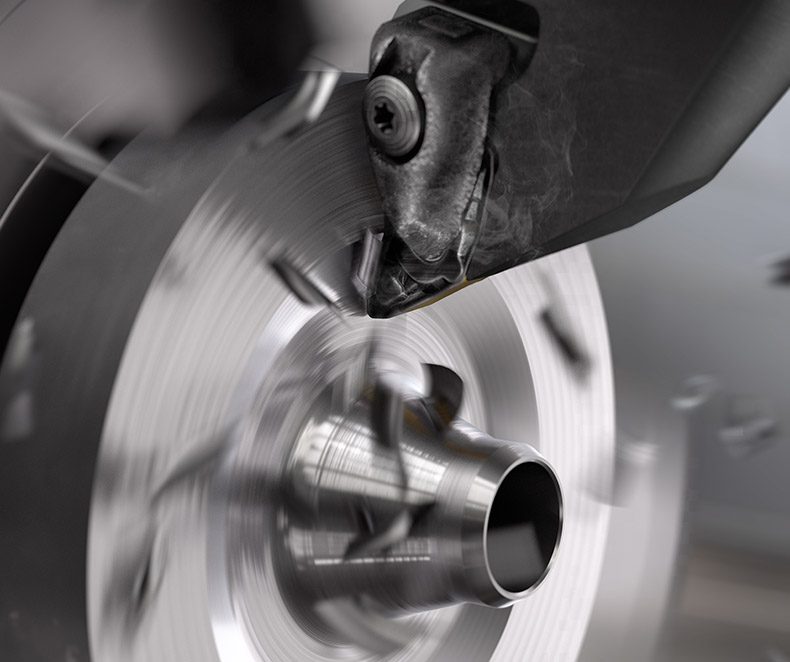
The Coromill® Dura end mills work in a wide range of applications and materials.
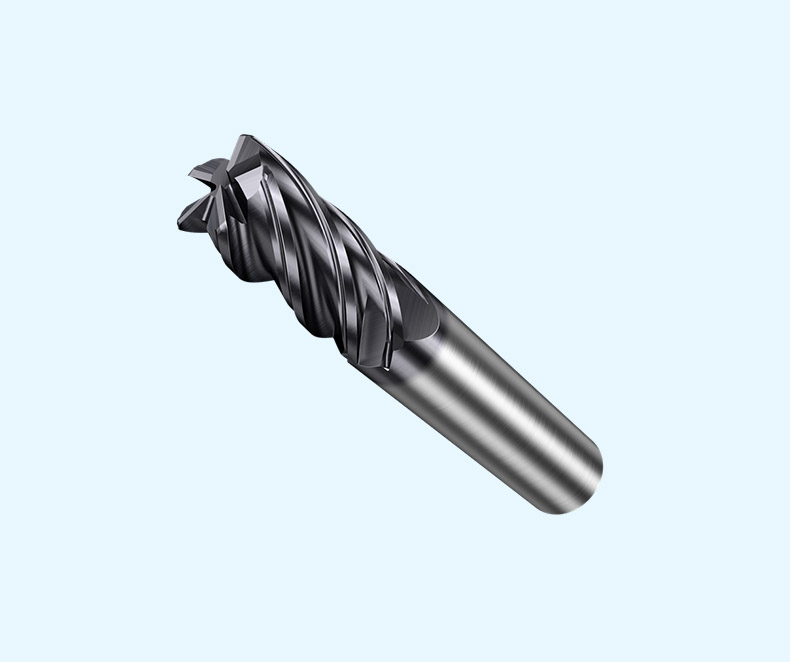